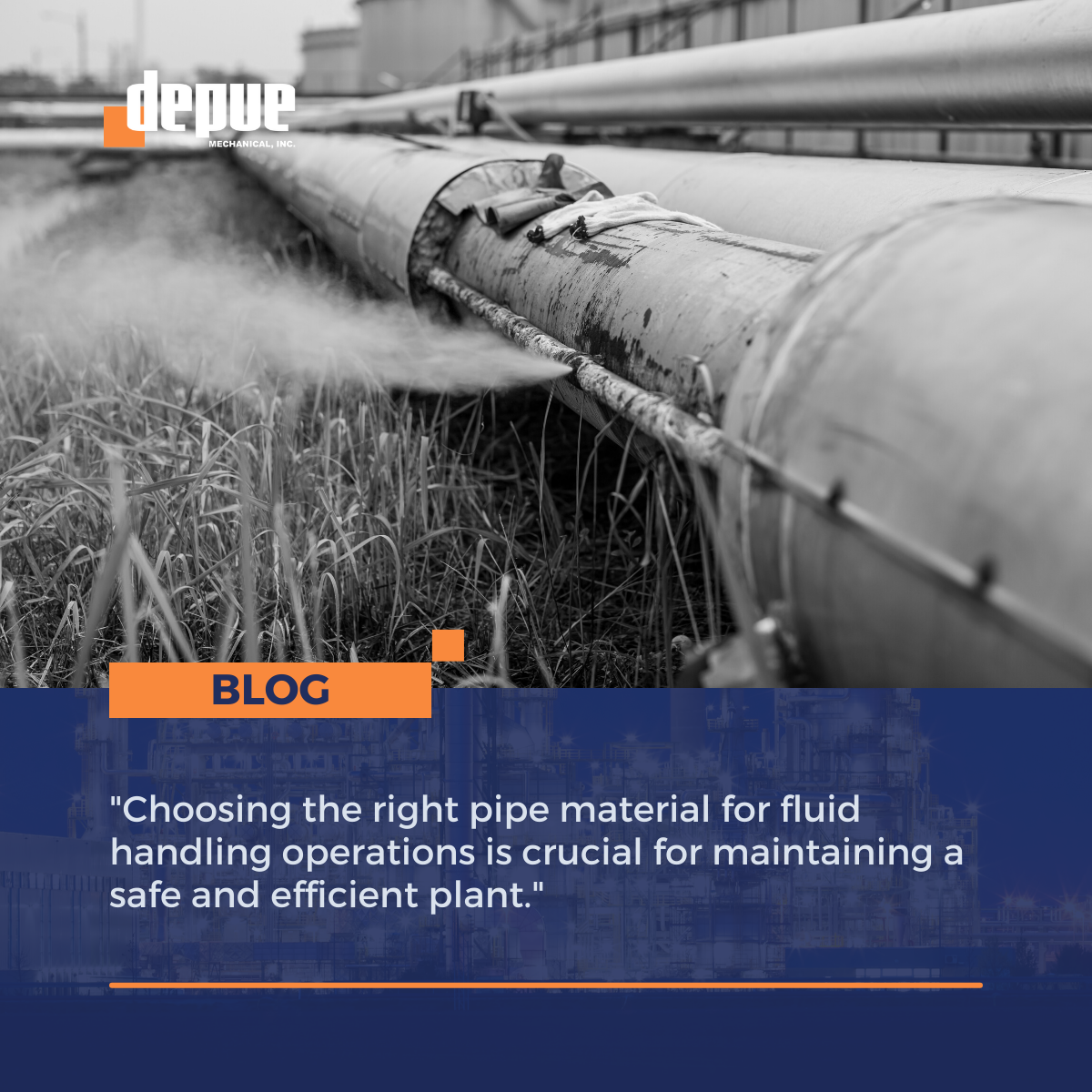
Choosing the right pipe material for fluid handling operations is essential for maintaining a safe and efficient chemical plant. With so many options available, it can be overwhelming to determine which one is the best fit for your specific needs – be it a new build, moving systems, or replacing a line.
Before you or your contractor choose a pipe for your system, take the following factors into account so you can make an informed decision and ensure the longevity and reliability of your fluid handling system.
To make your planning easier, we’ve put together a list of what to consider before selecting the right type of pipe for your operations.
In this article, we’re going to discuss these 5 things to consider:
- The Pressure of Liquid Passing Through
- The Temperature of Liquid Passing Through
- Service Life of the Fluid Handling System
- Exposure to External Elements
- Ease of Maintenance
The Pressure of the Liquid Handling Process
The pressure of your fluid handling process will determine which pipe material is best for you. For example, if you’re working with ammonia or chlorine gas, you’ll need to ensure that your piping can withstand high pressures.
If your service fluids have high pressure, you need a piping material that can withstand it. This can be achieved by selecting either a high-strength material, a higher thickness material, or a material designed to resist high-pressure fluids. The typical maximum pressure for most manufacturing facilities’ piping is around 150 pounds per square inch gauge (psig). If you need to handle fluids with higher pressures than this, a specially designed piping material may be necessary.
Fluids and gases have different pressure levels inside the piping system, and the type of fluid being handled will determine the pressure levels required. Cryogenic fluids, for example, create high-pressure environments during the transfer process. Other external factors, such as temperature and elevation, can also impact the pressure levels inside the piping system.
Other liquids and gases that might require high-pressure pipe materials include:
- Propane (-42C)
- Carbon dioxide (-78C)
- Nitrous oxide (-88C)
- Acetylene (3251F/1860C)
- Butane (572F/300C)
- Hydrogen (2032F/1130C)
It is crucial to choose a pipe material that can handle substances and conditions with high or low pressure ratings. If you use a pipe that is not suitable for high-pressure handling, you run the risk of experiencing leaks, pipe bursts, flooding, fire, explosion, and injuries to personnel or property.
Do not assume that your fluid handling system is capable of handling high-pressure substances. Always consult with your contractor to determine whether your fluid handling system is designed to handle high-pressure fluids and vapors before putting them to use.
The Temperature of Liquid Passing Through
When considering your fluid handling system, it is important to take into account the temperature of the liquid being transported. If you are handling high-temperature liquids, it is essential to ensure that your system is composed of high-temperature pipe materials. Plastic piping may not be ideal for handling high temperatures, whereas metal pipe materials are generally a better choice for high-temperature liquids, although some types may become too hot to handle.
If you are dealing with extremely high or low-temperature fluids, including cryogenic liquids, it is crucial to use materials specially designed for extreme temperature ranges. Failure to do so could result in damage or corrosion to your pipes, contamination of the liquids inside them, and even pipe breakage, which can lead to costly repairs, damaged products, and hazardous working conditions. While metal pipe materials are typically suitable for extremely hot liquids, caution should be exercised when working with them. Depending on the temperature, aluminum may be the best choice for transporting cryogenic liquids.
Your piping material must be able to withstand and maintain these temperatures throughout the liquid transfer process. In many applications, precise temperatures are required for all liquids and vapors used, including laboratories, food processing, medical facilities, and plants that work with hazardous chemicals.
Various materials can be suitable for high-temperature applications, such as carbon steel, PTFE, PVDF, ATL PTFE, and PP pipe linings. For extremely low temperatures, copper, certain aluminum alloys, and high-alloy austenitic stainless steel are the least likely to become brittle and break.
Service Life of the Fluid Handling System
When choosing piping for your fluid handling system, it’s important to consider how long you expect the system to last. If you anticipate having to replace the system in five to ten years for reasons such as relocation, investing in a highly durable piping material may not be necessary. This can also impact your budget and the type of material you choose.
However, if you expect the system to last for ten years or more, it’s best to invest in the most durable piping material available.
For instance, temporary worksites or processing plants that do not frequently handle fluids may not require as durable a system as a permanent plant that handles fluids every day. Additionally, it’s important to consider how frequently your business will use the fluid handling system. In some cases, extremely corrosive chemicals, hazardous materials, or temperature-sensitive fluids may require specific pipe materials, regardless of the desired service life of your system. If no special circumstances apply to your business, this information can help you determine how much to invest in your pipes and the type and quality of material to use.
Exposure to External Elements
External factors can pose a threat to fluid handling systems both indoors and outdoors. Indoors, external corrosion and other issues may arise from corrosive fumes, humidity, and mold. Meanwhile, outdoor threats include seawater, harsh weather, microorganisms, and plant growth, among others.
If any part of your fluid handling system is exposed to the outdoors, it’s essential to select piping material that can withstand environmental elements. External factors that can lead to corrosion or deterioration of your fluid handling piping consist of UV light, corrosive soil, precipitation, and other atmospheric conditions. It is important to exercise caution when dealing with external elements such as:
- Corrosive fumes or vapors from other workstations or materials
- Extreme or changing temperatures, whether indoors or outdoors
- Mold and mildew growth
- Salt from seawater
- Inclement weather, such as rain, snow, lightning, and hail
- Microorganisms, including those that can corrode or burrow
- Plant growth, roots, and moss on outdoor piping
- Exposure to UV rays from the sun
- Corrosive and damp soil
Ease of Maintenance
Before deciding on a piping material, you should know that there are piping materials that are easier to clean than others. It is important to consider how often you can realistically clean your fluid handling system, as it can be a time-consuming task depending on the size and complexity of your system. If regular cleaning is not feasible, prioritizing a low-maintenance piping material is crucial for your facility.
Ensure that the material you choose for your fluid handling pipes is maintainable based on your current circumstances. There are three types of maintenance that all fluid handling systems should consider:
- Routine cleaning maintenance: This will prevent internal and external product build-up, which can corrode your system and contaminate transferred fluids.
- Preventive maintenance: This should be performed at regularly scheduled intervals based on the approximate cost of downtime, potential risks of system failure, expected time between part repairs, and availability of backup equipment if necessary.
- Emergency maintenance: Even with preventive maintenance and durable products, emergency or special repairs may be necessary at some point. Address concerns promptly to reduce emergency maintenance visits.
In each of these maintenance scenarios, your pipes need to be easily accessible. It is recommended to have a professional contractor install your fluid handling system. They will consider your system as a whole and ensure your pipes are appropriately sized for your space and business needs, without being too large and resulting in unnecessary maintenance or loss of usable space.
If your business cannot accommodate regular and frequent maintenance due to time, workforce, or budget constraints, choosing a low-maintenance piping material should be your top priority.
Remember: Safety and Efficiency is Everything
In conclusion, choosing the right pipe material for fluid handling operations is crucial for maintaining a safe and efficient plant. By considering the temperature of the liquid passing through, the pressure of the liquid handling process, the service life of the fluid handling system, the ease of maintenance, and exposure to external elements, you can make an informed decision that ensures the longevity and reliability of your fluid handling system.
Remember to consult with experts to determine which materials are best suited for your specific needs. With careful consideration and planning, you can select the ideal pipe material and ensure the success of your fluid handling operations for years to come.
If you are unsure of which pipe material would be best for your fluid handling system, or are looking to discuss maintenance, connect with us.